A revolution in surgery :
Breaking the boundaries of traditional materials with Vulkalloys
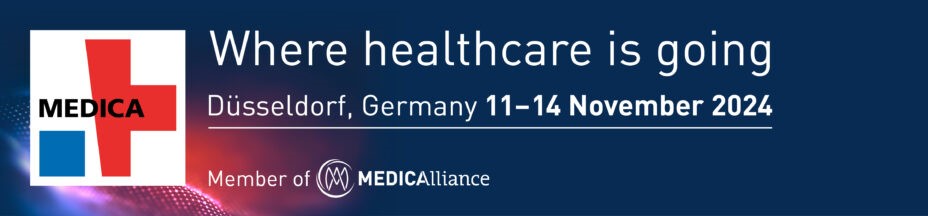
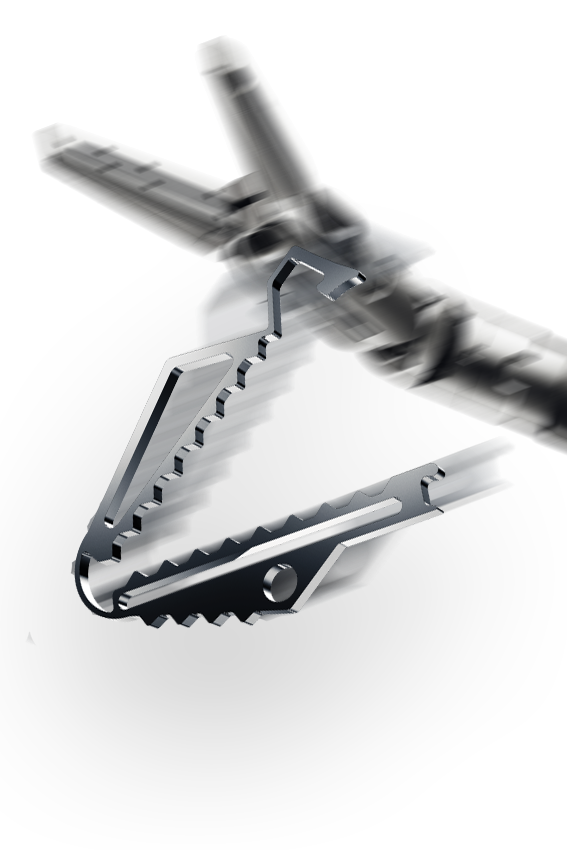
Current limitations in instruments designs.
The development of innovative surgical instruments, such as bipolar forceps, is hampered by limitations due to the properties of conventional materials such as stainless steels and titanium.
These materials have mechanical characteristics that restrict miniaturisation, durability and patient safety.
Current manufacturing processes require complex technical skills, compromising the precision and reproducibility of medical device components.
The solutions provided by Vulkalloys®
✔ 3 times greater resistance than grade 5 titanium
for unrivalled miniaturisation capacity.
✔ 2 times greater deformation without brittleness
to increase safety.
✔ Resistance to fatigue
to boost performance overtime.
✔ High hardness and unrivalled wear resistance
to boost performance overtime.for increased durability.
✔ Their biocompatibility and non-magnetism
for the design of medical instruments and devices.
In addition, the possibility of using thermo-moulding eliminates the need for machining and offers a new capacity for designing innovative geometries, while making significant savings in terms of materials and ressources. It also ensures a high level of dimensional accuracy and surface finish, combined with excellent industrial reproducibility.
The VulFAB2025 series
The company has achieved a significant milestone in its industrial program by raising over €30 million in December 2023 to industrialize its amorphous metals processing technologies, from casting to the final part manufacturing. The company is ready to support its customers’ development by offering solutions for producing amorphous metal components tailored to their product designs. It already has the capability to produce parts for Medtech and various other sectors such as aerospace, watchmaking, and micromechanical industries, including supplying samples for further analysis, prototype design, and series production qualification. Starting in 2026, the company will commence mass production of amorphous metal parts at its first 2,500 m² plant near Grenoble, France.
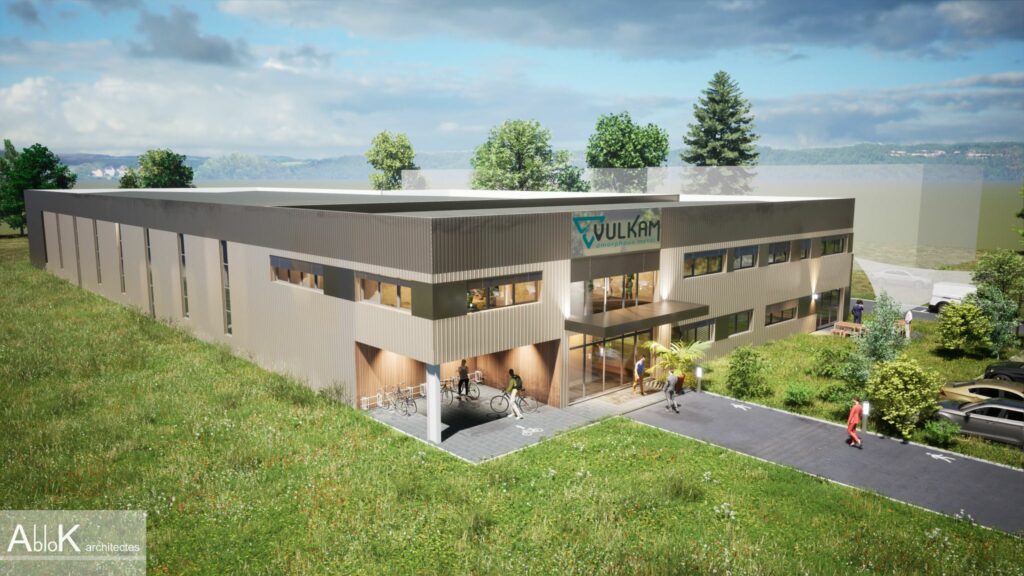